En Vygon, las máquinas de envasado aúnan productividad, seguridad y automatización
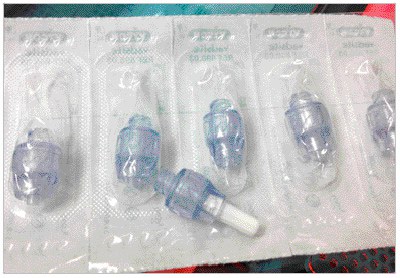
Especializada en los dispositivos médicos estériles de uso único (1), la empresa familiar Vygon, que ha celebrado su 50 aniversario el año pasado, ha adquirido una reputación internacional, sobre todo con una de sus especialidades: los catéteres. Con seis fábricas (tres de ellas en Francia: SIPV, SAP y SIPA), una en Alemania, una en Bélgica y dos fuera de Europa (Colombia - 1998 y Estados Unidos - 2007) realizó el año pasado una cifra de negocios de 253 millones de euros (243 millones de euros en el 2011), y marca una progresión de margen y un resultado "muy estimables". La empresa invierte hasta 7% de su cifra de negocios.
(1) Empleados en los campos
de la neonatología, pediatría, anestesia, tratamiento del dolor,
urgencias, cuidados intensivos, sala de operaciones y oncología
En un sector en que la competitividad se hace cada vez más dura, sobre todo en cuanto a precios se refiere, la empresa sigue creciendo "aunque seamos muy probablemente los más caros del mercado" reconoce Eric Trellu, director de Méthodes Centrales Industrialisations - MCI. ¿A qué se debe esta paradoja francesa? A varias razones.
Su crecimiento se debe a una gran escucha del mercado, llevada a cabo por un servicio de marketing y comercial de proximidad. Así, los nuevos productos lanzados para los profesionales de los cuidados a domicilio en el 2009, los HAD - Hospitalización a domicilio - de sets compuestos por dispositivos estándar marcan una progresión de 10% por año.
La esterilización en Vygon Todos los productos fabricados por Vygon se esterilizan por sistema. Con el refuerzo de la legislación, la empresa decidió, hace 10 años, centralizar en Europa la operación de esterilización en una única planta. Ubicada en Verneuil-en-Halatte, la planta cuenta con cuatro autoclaves, cada una con una capacidad de hasta 30 paletas (el equivalente de un tráiler) para una sola operación. El ciclo de esterilización, realizado mediante óxido de etileno dura 22 horas. La esterilización se asegura mediante una etiqueta pegada sobre todas las cajas que entran en la autoclave. Al salir, la etiqueta cambia de color. La planta cuenta con una superficie de 13500 m2 de almacenamiento de paletas. |
Un crecimiento también gracias a una integración total de todas sus actividades. La empresa diseña sus dispositivos, transforma los plásticos (por extrusión e inyección), monta, envasa, esteriliza y comercializa ella misma todo lo que produce (exceptuando gran parte de sus campos de operaciones). Esta integración de toda la cadena de valor se apoya sobre tres pilares fundamentales, que son la innovación con dos centros de investigación, la seguridad y la calidad. "Nuestros clientes están dispuestos a pagar más para obtener lo mejor", recalca el director - MCI.
Y lo mejor radica sobre todo en la validación por el laboratorio central de Vygon, ubicado en Acoquen, de todos sus productos (materiales y componentes) fabricados por todas sus fábricas; cada planta dispone además de un responsable de calidad. El laboratorio comprueba la compatibilidad de todos los materiales (PVC, PE, policarbonato, poliuretano, PUR, POM,...) que forma parte de la composición de las piezas que constituyen un catéter, hasta su montaje. Desde hace tres años, estudia nuevas moléculas de sustitución del BPA que quedará prohibido en el 2015 para los dispositivos médicos.
Por su parte, el servicio MCI, que cuenta con 35 personas, dispone de un taller de I + D para evaluar cualquier proceso nuevo. Equipado con cuatro presas, de las que una es de silicona líquida, evalúa sobre todo el comportamiento de los materiales plásticos, la mecanización, los prototipos de moldes de montaje. "Estamos estudiando un nuevo catéter arterial para el mercado alemán e inglés con una nueva automatización. Estamos en fase de pruebas desde hace un año, tanto a nivel del diseño de la producción como del montaje", añade E. Trellu.
Lo mejor pasa también por una gran industrialización de los procesos asociados a una automatización cada vez más elevada de las maquinas. "Un requisito necesario para producir calidad y seguir produciendo en Europa", recalca nuestro interlocutor. Esta estrategia industrial se apoya sobre un nivel de control y de seguimiento extremadamente riguroso que hemos reforzado aun más desde hace tres años.
"Cada país tiene su interpretación de las legislaciones en vigor, y los clientes extranjeros piden controles más exhaustivos", observa el director. Dado que la empresa exporta a todo el mundo, refuerza su nivel de control más allá del campo reglamentario y normativo europeo. En cada máquina de montaje, cada operación está controlada mediante medios específicos a medida y cada vez por sistemas de visión. "Contamos en nuestra empresa con dos personas dedicadas a la visión, además de los acuerdos con empresas especializadas", puntúa E. Trellu. Aunque la visión sea omnipresente en Vygon, la empresa empieza a implementar otros sistemas de control que pasan por el recuento y la dosificación de las piezas al miligramo.
En Vygon, se hace todo lo posible para acelerar la automatización y la productividad. De esta manera, cada máquina de montaje está asociada a una línea de envasado, como lo ilustra la reciente instalación de la que monta un conector de larga duración compuesto por tres piezas a una cadencia de 250 piezas/min. (15000 piezas/hora) y las envasa por grupos de 20 piezas en un único blíster flexible a una velocidad de 18000 piezas/hora, con un buffer de 20 minutos de autonomía entre ambas máquinas para evitar cualquier corte de productividad. Una línea estudiada con ULMA Packaging con la que Vygon trabaja desde hace cinco años. Actualmente, el grupo dispone de 13 máquinas del constructor español. Recientemente, se ha instalado una segunda línea de termoformado multiformatos con cambio rápido de herramientas en Ecouen, y la tercera saldrá pronto hacia Colombia para sustituir una máquina más antigua de un constructor alemán.
"Reconozco que mi primer contacto con ULMA venía motivado por el precio, un criterio que no se puede menospreciar dado que necesitábamos entonces tres máquinas nuevas para colocarlas en salida de tres máquinas de montaje nuevas. Y según íbamos hablando, hemos descubierto que el constructor integraba en sus máquinas bases y componentes estándar. Un argumento que ha jugado muy a su favor. Esta estandarización nos hace menos dependientes del constructor, ya que en caso de avería, todo va más rápido. También nos atrajo su apertura de espíritu y su escucha de los clientes", añade el director. "No queremos volver a nuestros clientes dependientes", contesta Philippe Desbordes, director comercial y de comunicación de ULMA Packaging Francia. "Asimismo, si nos piden un sistema particular, lo integramos sin problemas ya que hemos establecido numerosas colaboraciones en este ámbito", como ha sido el caso en Ecouen, donde un PC industrial B&R ha sustituido otro sistema que proponía ULMA en su máquina. Así como el constructor analiza la necesidad de su cliente, incluso tratándose de solicitudes muy específicas. "Lo que nos permite progresar", analiza Philippe Desbordes.
La planta de Ecouen ha tenido que resolver una problemática particular de cambio de formatos. "La máquina la llevaban mujeres, lo que dificultaba el cambio de herramientas pesadas y que conllevaban largos de tiempos de parada de la máquina", cuenta el director - MCI. Por ello hemos entregado a ULMA un pliego de condiciones estudiado con las operadoras. El cambio de formato se hace actualmente en menos de 10 minutos, sin dificultad. En España, hemos apreciado el poder dialogar con todas las personas que intervenían en el estudio de nuestra máquina. Ha sido una auténtico intercambio", concluye E. Trellu.
Artículo extraído de Emballage Digest #575