Launch of the new ULMA FV 55 SD flow pack wrapping machines, featuring a hygienic design and manufactured according to USDA standards
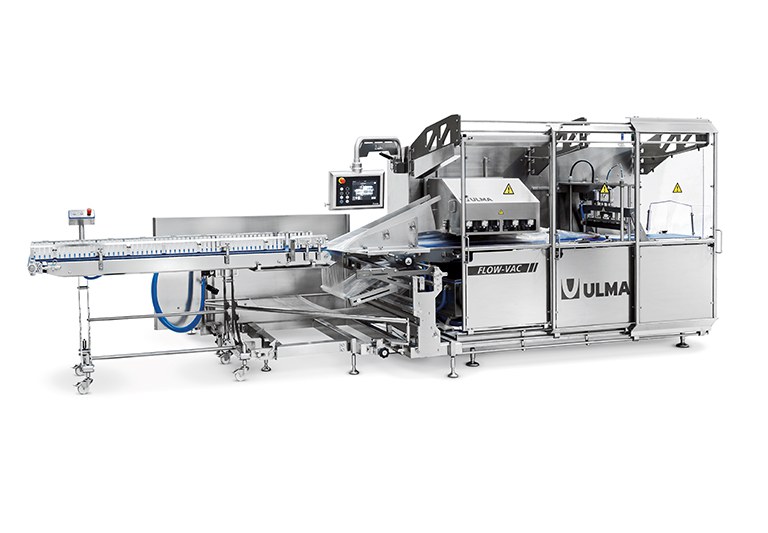
FLOW-VAC®: fully-automated solutions for the food industry
ULMA pioneered the FLOW-VAC® system in its search to meet its customers' automation, productivity, efficiency and packaging safety needs in the food industry, and has for many years offered FLOW-VAC® wrapping machines for automatic packaging of cheese, meat fresh cuts and processed meat, all with full reassurance in terms of safety while saving operational costs and improving productivity.
The FLOW-VAC® system automatically places the products to be packaged in the bag created by the packaging machine, and transfers them to a vacuum system in sync with the production line. The system adapts the length of the bag to the length of the product, therefore optimising the use of packaging material, and allows a quick, easy changeover between formats, optimising the packaging process.
Fewer costs and risks, higher productivity and hygiene
The system can be operated by a single operator, while its operation is compatible with the rest of his tasks which minimises labour and increases productivity. This avoids direct handling of food during packaging, thus lessening the risk of contamination and reducing vacuum losses from packaging. FLOW-VAC® wrapping machines not only guarantee maximum hygiene and food safety conditions but also, by adjusting the film in line with product size, improve the packaging's final appearance, save material during wrapping, and optimise stock levels. Three aesthetic, logistics and environmental benefits that make them the most cost-effective solution, particularly for customers with high production needs.
New FV 55 SD with hygienic design, more accessible and easier to clean
The new FV 55 SD model features a hygienic design and is the latest development to form part of ULMA Packaging's FLOW-VAC® wrapping machine catalogue. It has been developed according to USDA standards, the most demanding in the food industry.
FV 55 SD wrapping machines with hygienic design are built to avoid any build-up of water, dust or dirt, thus preventing the growth of bacteria and microorganisms and making them easier to clean.
Their design ensures easy cleaning and sanitising, with easy-release conveyor belts for easier maintenance and cleaning and to clean the cross sealing jaws.
The feeding conveyor, which is the area requiring the highest cleaning and sanitation processes, has IP66 protection rating. It can be dismantled without the use of any tools and allows moving to a cleaning area.
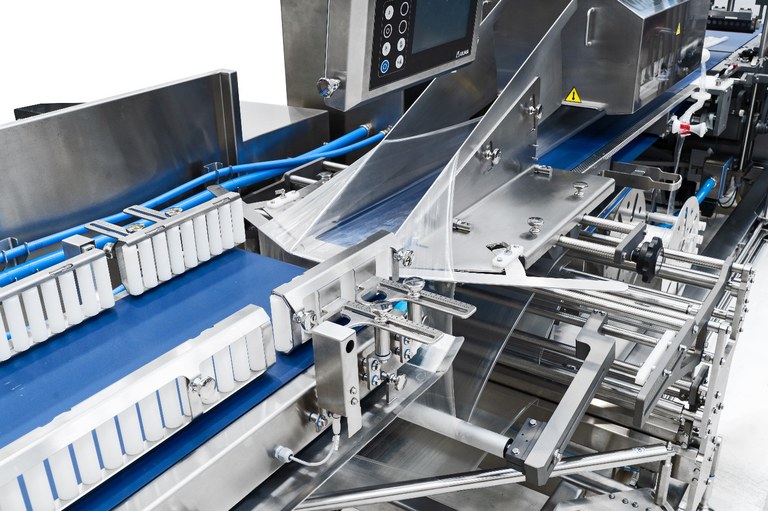
Close-up of the feeder conveyor.
The packaging machine is designed with IP65 rating in order to work in high humidity conditions and withstand aggressive working environments. It has an electrical cabinet with double protection to ensure the electrical components are protected from water ingress, and the knives are easy to change without any tools.
HMI
Machine control is based on state-of-the-art HMI systems, such as ULMA's in-house industrial PC, known as UPC, or Rockwell Automation's Allen-Bradley PLC.
These systems ensure the wrapping machine has a wide range of connectivity options and is straightforward and intuitive to use. They include machine and production settings adjustment wizards, data and production parameter control, and customisable instructions in a range of formats (step-by-step, PDF and video).
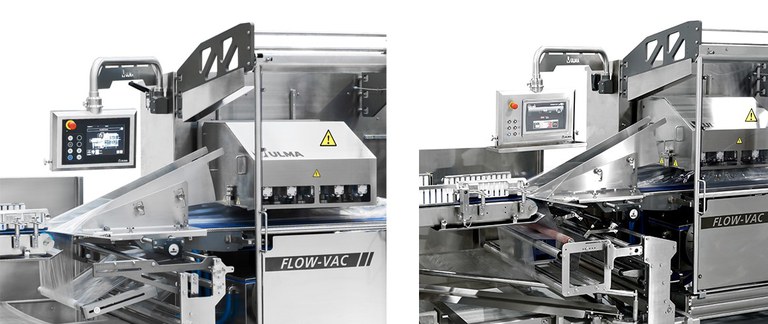
Detail of HMI with UPC control (left) and Allen-Bradley control (right).
The most cost-effective solution for customers with high production needs
ULMA's new FV 55 SD flow pack wrapping machines are easy to use and clean, meet the most demanding standards in the food industry, improve final product appearance, save material during wrapping, and optimise packaging material stock levels and logistics.
In short, they are the most profitable solution for customers with high production needs who are looking for a hygienic, safe packaging system for vacuum wrapping meat or cheese products, improving productivity and maximum reassurance.